The premier information and solutions provider to Canada's construction industry
Evaluate, choose and prepare projects, forecast growth, and stay informed about the industry through leading technology.
Learn moreTake control of your pipeline with the smartest digital bid board
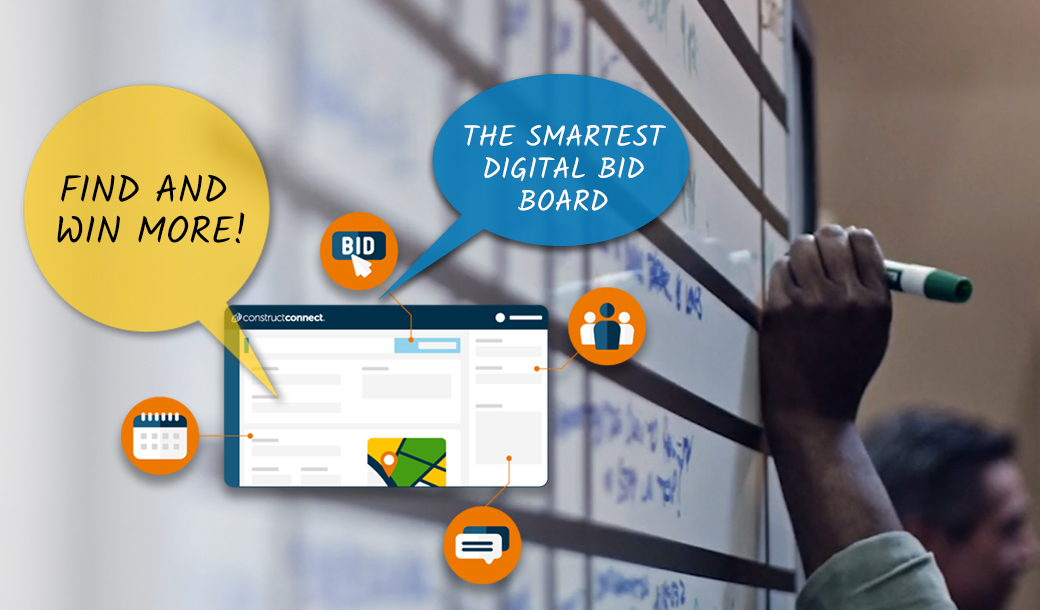
The right project leads to fuel your success.
All your bids, and your entire team,
in one workspace. Instant updates
prioritized and ranked automatically.
Find and win more with the largest
ITB & project data network.
Software built for the people who do the work
Your trusted source for industry news and project information
Expert insight into construction's economic future
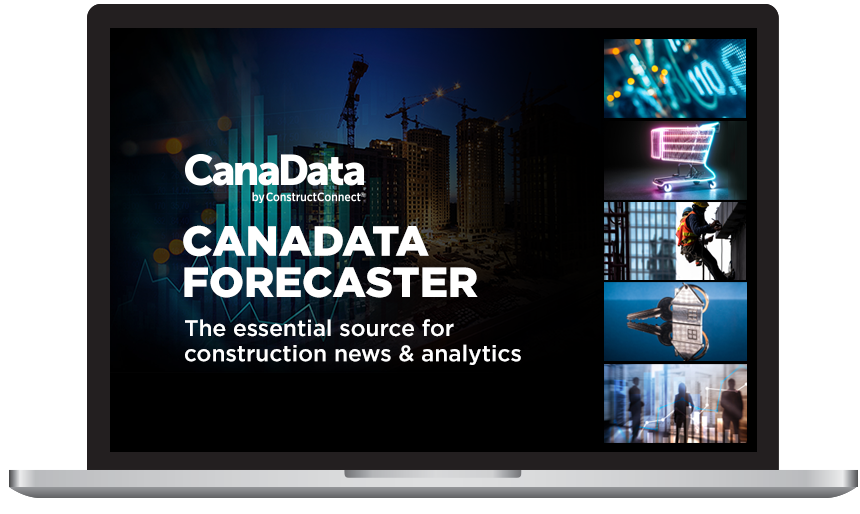
CanaData Forecaster
Get daily updates and easy-to-grasp information on main economic indicators and building activity measures
View Economic News & ChartsCanada's building design newsletter
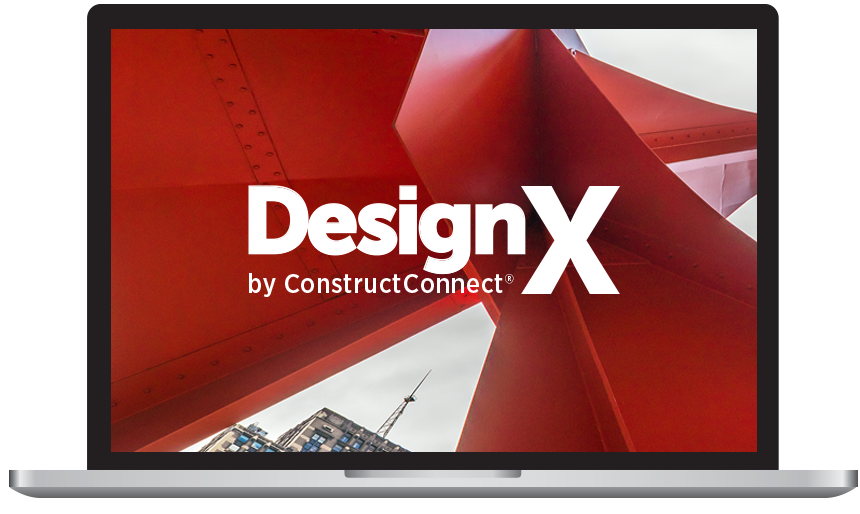
Top architecture and engineering news delivered to your inbox
Get a first look at the latest trends, innovations and thought leadership from the industry's movers and shakers.
Subscribe nowCanada's No. 1 construction industry podcast
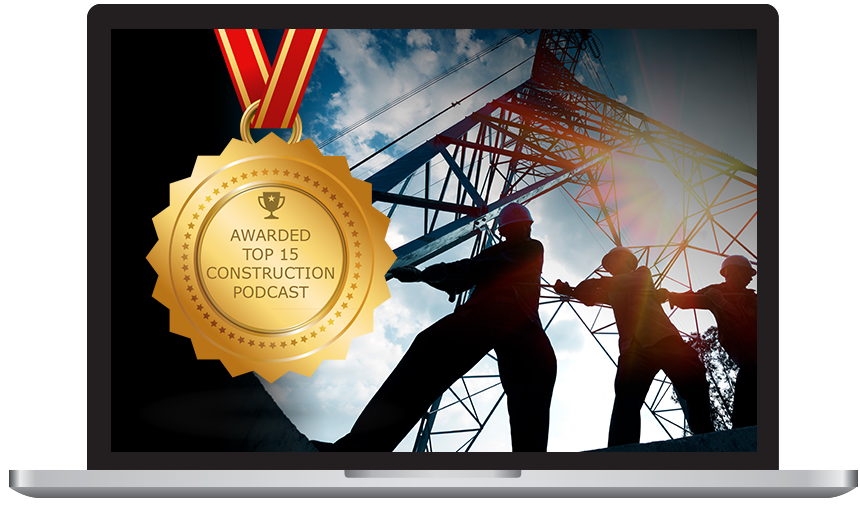
Go behind the story with The Construction Record, Canada's leading podcast for in-depth construction industry news and trends.
Listen to episodes